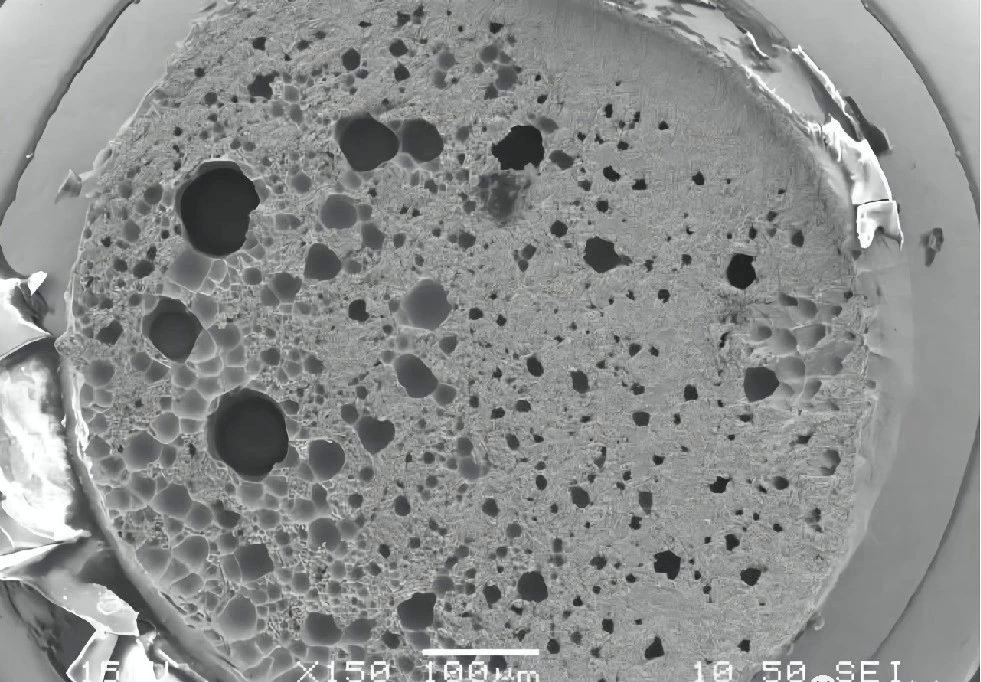
1 Giới thiệu
Trong quá trình lắp ráp bảng mạch, chất hàn được in trên miếng hàn của bảng mạch trước tiên, sau đó dán các linh kiện điện tử khác nhau. Cuối cùng, sau lò nung lại, các hạt thiếc trong kem hàn được nấu chảy và tất cả các loại linh kiện điện tử và miếng hàn của bảng mạch được hàn lại với nhau để thực hiện việc lắp ráp các mô-đun con điện. Công nghệ gắn bề mặt (sMT) ngày càng được sử dụng nhiều trong các sản phẩm đóng gói mật độ cao, chẳng hạn như gói cấp hệ thống (siP), thiết bị ballgridarray (BGA) và Chip trần nguồn, gói phẳng vuông không có chốt (quad aatKhông chì, được gọi là QFN ) thiết bị.
Do đặc điểm của quá trình và vật liệu hàn dán, sau khi hàn nóng chảy lại các thiết bị có bề mặt hàn lớn này sẽ xuất hiện các lỗ trên khu vực hàn hàn, điều này sẽ ảnh hưởng đến tính chất điện, tính chất nhiệt và tính chất cơ học của Hiệu suất sản phẩm, và thậm chí dẫn đến hư hỏng sản phẩm, do đó, việc cải thiện khoang hàn nóng chảy lại bằng kem hàn đã trở thành một vấn đề về quy trình và kỹ thuật cần phải giải quyết, một số nhà nghiên cứu đã phân tích và nghiên cứu nguyên nhân gây ra khoang hàn bóng hàn BGA và đưa ra các giải pháp cải tiến, hàn thông thường. dán quá trình hàn nóng chảy lại khu vực hàn của QFN lớn hơn 10 mm2 hoặc diện tích hàn lớn hơn 6 mm2 thì thiếu giải pháp hàn chip trần.
Sử dụng hàn Preformsolder và hàn lò hồi lưu chân không để cải thiện lỗ hàn. Chất hàn đúc sẵn đòi hỏi thiết bị đặc biệt để định vị từ thông. Ví dụ, chip bị lệch và nghiêng nghiêm trọng sau khi chip được đặt trực tiếp lên vật hàn đúc sẵn. Nếu chip gắn thông lượng được phản xạ lại và sau đó điểm, quá trình này sẽ tăng thêm hai phản xạ lại, và chi phí của vật liệu hàn và vật liệu thông lượng đúc sẵn cao hơn nhiều so với dán hàn.
Thiết bị hồi lưu chân không đắt hơn, công suất chân không của buồng chân không độc lập rất thấp, hiệu suất chi phí không cao và vấn đề bắn thiếc nghiêm trọng, đây là yếu tố quan trọng trong ứng dụng mật độ cao và bước nhỏ các sản phẩm. Trong bài báo này, dựa trên quy trình hàn nóng chảy lại bằng kem hàn thông thường, một quy trình hàn nóng chảy thứ cấp mới được phát triển và giới thiệu để cải thiện khoang hàn và giải quyết các vấn đề về liên kết và nứt phốt nhựa do khoang hàn gây ra.
2 Hàn dán khoang hàn nóng chảy lại và cơ chế sản xuất
2.1 Khoang hàn
Sau khi hàn nóng chảy lại, sản phẩm được kiểm tra dưới tia X. Các lỗ ở vùng hàn có màu nhạt hơn được phát hiện là do chất hàn trong lớp hàn không đủ, như hình 1
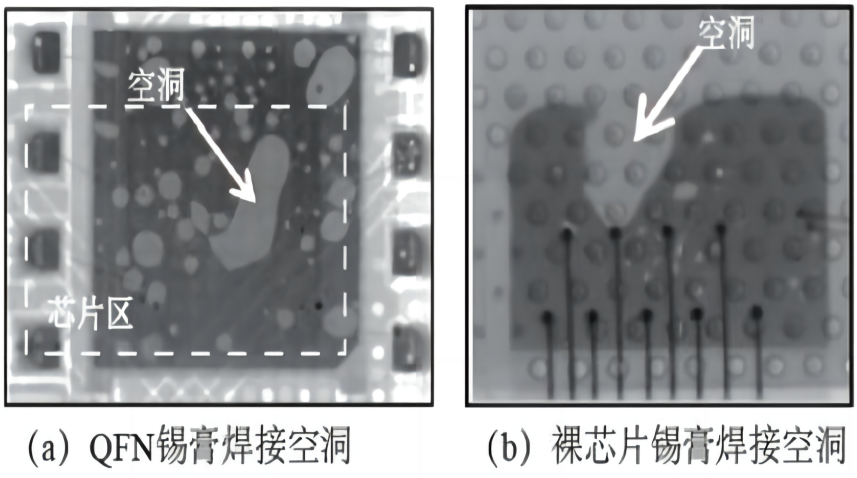
Phát hiện lỗ bong bóng bằng tia X
2.2 Cơ chế hình thành khoang hàn
Lấy kem hàn sAC305 làm ví dụ, thành phần và chức năng chính được thể hiện trong Bảng 1. Chất trợ dung và hạt thiếc được liên kết với nhau thành dạng dán. Tỷ lệ trọng lượng của chất hàn thiếc và chất trợ dung là khoảng 9:1 và tỷ lệ thể tích là khoảng 1:1.
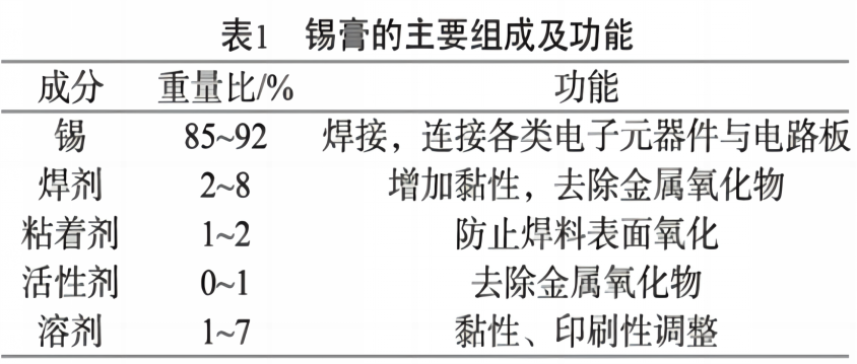
Sau khi miếng dán hàn được in và gắn với các linh kiện điện tử khác nhau, miếng dán hàn sẽ trải qua bốn giai đoạn làm nóng trước, kích hoạt, hồi lưu và làm mát khi đi qua lò hồi lưu. Trạng thái của chất hàn dán cũng khác nhau tùy theo nhiệt độ khác nhau ở các giai đoạn khác nhau, như trong Hình 2.
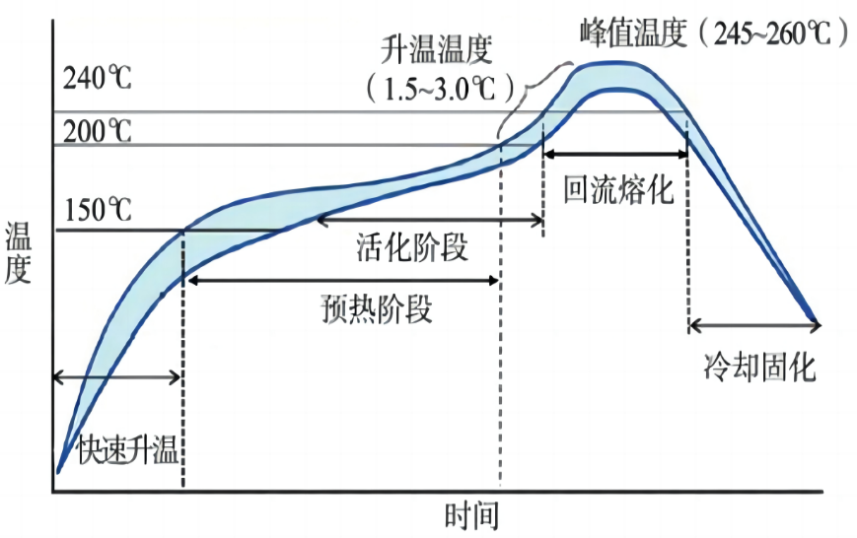
Tham khảo hồ sơ cho từng khu vực hàn nóng chảy lại
Ở giai đoạn làm nóng sơ bộ và kích hoạt, các thành phần dễ bay hơi trong chất trợ dung trong kem hàn sẽ bay hơi thành khí khi được nung nóng. Đồng thời, khí sẽ được sinh ra khi lớp oxit trên bề mặt lớp hàn bị loại bỏ. Một số khí này sẽ bay hơi và để lại kem hàn, đồng thời các hạt hàn sẽ bị ngưng tụ chặt do sự bay hơi của chất trợ dung. Ở giai đoạn hồi lưu, từ thông còn lại trong kem hàn sẽ bay hơi nhanh chóng, các hạt thiếc sẽ tan chảy, một lượng nhỏ khí dễ bay hơi từ thông và phần lớn không khí giữa các hạt thiếc sẽ không bị phân tán kịp thời và phần còn lại trong Thiếc nóng chảy và dưới sức căng của thiếc nóng chảy là cấu trúc bánh hamburger và bị giữ lại bởi miếng hàn bảng mạch và các linh kiện điện tử, đồng thời khí bọc trong thiếc lỏng khó thoát ra ngoài chỉ nhờ lực nổi hướng lên. Thời gian nóng chảy trên rất ngắn. Khi thiếc nóng chảy nguội đi và trở thành thiếc rắn, các lỗ rỗng xuất hiện trong lớp hàn và các lỗ hàn được hình thành, như thể hiện trên Hình 3.
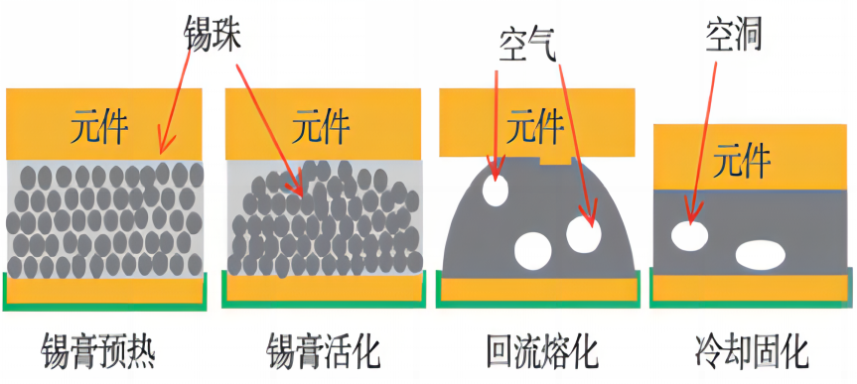
Sơ đồ khoảng trống được tạo ra bởi hàn nóng chảy dán hàn
Nguyên nhân sâu xa của khoang hàn là do không khí hoặc khí dễ bay hơi bọc trong kem hàn sau khi tan chảy không được thải ra hoàn toàn. Các yếu tố ảnh hưởng bao gồm vật liệu dán hàn, hình dạng in dán hàn, lượng in dán hàn, nhiệt độ hồi lưu, thời gian hồi lưu, kích thước hàn, cấu trúc, v.v.
3. Kiểm định các yếu tố ảnh hưởng của lỗ hàn nóng chảy in dán hàn
Các thử nghiệm QFN và chip trần đã được sử dụng để xác nhận nguyên nhân chính gây ra các khoảng trống hàn nóng chảy lại và tìm cách cải thiện các khoảng trống hàn nóng chảy lại được in bằng keo hàn. Hồ sơ sản phẩm hàn phản xạ dán chip trần và QFN được thể hiện trong Hình 4, kích thước bề mặt hàn QFN là 4,4mmx4,1mm, bề mặt hàn là lớp đóng hộp (thiếc nguyên chất 100%); Kích thước hàn của chip trần là 3,0mmx2,3mm, lớp hàn là lớp lưỡng kim niken-vanadi phún xạ, và lớp bề mặt là vanadi. Tấm hàn của chất nền được nhúng vàng niken-palađi điện phân và độ dày là 0,4μm/0,06μm/0,04μm. Sử dụng kem hàn SAC305, thiết bị in kem hàn là DEK Horizon APix, thiết bị lò hồi lưu là BTUPyramax150N và thiết bị chụp X-quang là DAGExD7500VR.
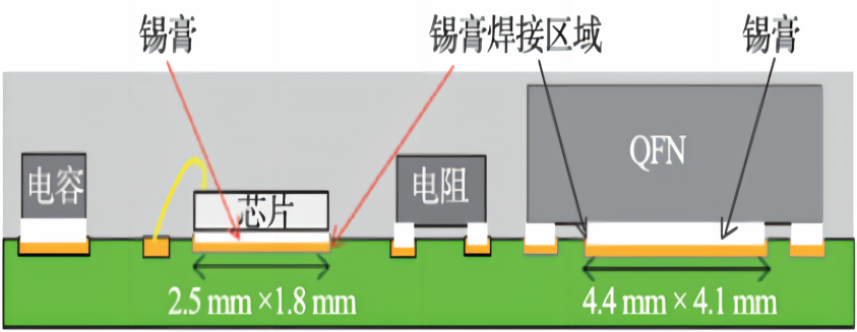
Bản vẽ hàn chip trần và QFN
Để thuận tiện cho việc so sánh các kết quả thử nghiệm, hàn nóng chảy lại được thực hiện trong các điều kiện trong Bảng 2.
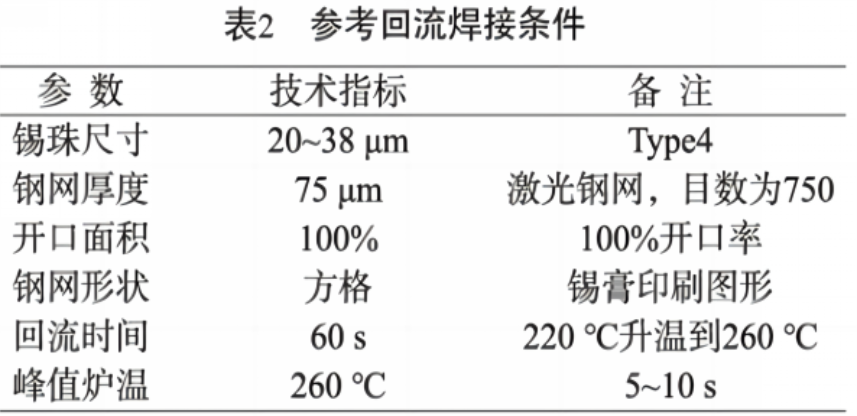
Bảng điều kiện hàn Reflow
Sau khi hoàn tất quá trình lắp bề mặt và hàn nóng chảy lại, lớp hàn được phát hiện bằng tia X và người ta phát hiện có các lỗ lớn trên lớp hàn ở dưới cùng của QFN và chip trần, như trong Hình 5.
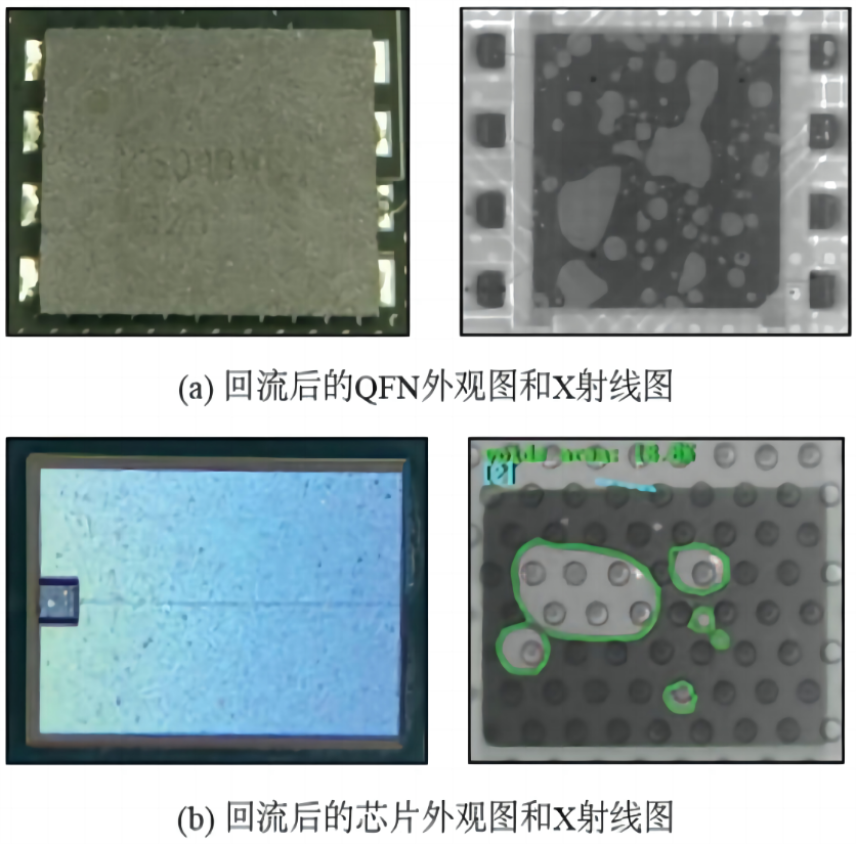
Hình ba chiều QFN và Chip (X-quang)
Vì kích thước hạt thiếc, độ dày lưới thép, tốc độ diện tích mở, hình dạng lưới thép, thời gian hồi lưu và nhiệt độ lò cao nhất sẽ ảnh hưởng đến các khoảng trống hàn nóng chảy lại, nên có nhiều yếu tố ảnh hưởng sẽ được xác minh trực tiếp bằng thử nghiệm DOE và số lượng thử nghiệm. các nhóm sẽ quá lớn. Cần nhanh chóng sàng lọc, xác định các yếu tố ảnh hưởng chính thông qua kiểm định so sánh tương quan, sau đó tối ưu hóa hơn nữa các yếu tố ảnh hưởng chính thông qua DOE.
3.1 Kích thước lỗ hàn và hạt thiếc dán hàn
Với thử nghiệm dán hàn SAC305 loại 3 (cỡ hạt 25-45 μm), các điều kiện khác không thay đổi. Sau khi hàn lại, các lỗ trên lớp hàn được đo và so sánh với kem hàn loại 4. Người ta nhận thấy rằng các lỗ trên lớp hàn không khác biệt đáng kể giữa hai loại kem hàn, cho thấy rằng kem hàn có kích thước hạt khác nhau không có ảnh hưởng rõ ràng đến các lỗ trong lớp hàn, đây không phải là yếu tố ảnh hưởng, như thể hiện trên hình. 6 Như được hiển thị.
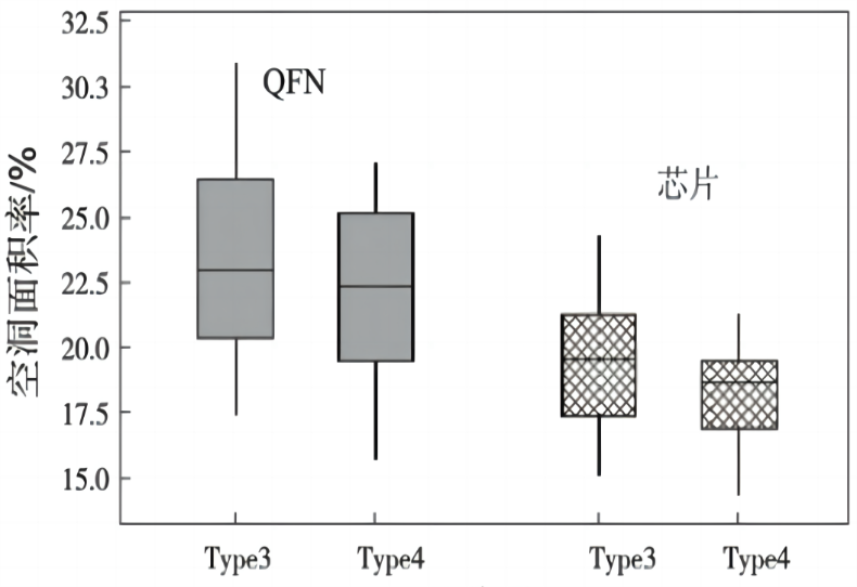
So sánh lỗ bột thiếc kim loại với các kích cỡ hạt khác nhau
3.2 Độ dày khoang hàn và lưới thép in
Sau khi hàn lại, diện tích khoang của lớp hàn được đo bằng lưới thép in có độ dày 50 μm, 100 μm và 125 μm, các điều kiện khác không thay đổi. Người ta thấy rằng ảnh hưởng của độ dày khác nhau của lưới thép (dán hàn) lên QFN được so sánh với ảnh hưởng của lưới thép in có độ dày 75 μm. Khi độ dày của lưới thép tăng lên, diện tích khoang giảm dần từ từ. Sau khi đạt đến độ dày nhất định (100μm), diện tích khoang sẽ đảo ngược và bắt đầu tăng lên khi độ dày của lưới thép tăng lên, như trong Hình 7.
Điều này cho thấy khi lượng kem hàn tăng lên, thiếc lỏng bị trào ngược sẽ bị chip bao phủ và lối thoát khí dư chỉ bị thu hẹp ở bốn phía. Khi lượng kem hàn thay đổi, lối thoát khí dư cũng tăng lên và luồng không khí tức thời được bọc trong thiếc lỏng hoặc khí dễ bay hơi thoát ra khỏi thiếc lỏng sẽ khiến thiếc lỏng bắn tung tóe xung quanh QFN và chip.
Thử nghiệm cho thấy khi độ dày của lưới thép tăng lên, vụ nổ bong bóng do không khí thoát ra hoặc khí dễ bay hơi cũng sẽ tăng lên và xác suất thiếc bắn ra xung quanh QFN và chip cũng sẽ tăng tương ứng.
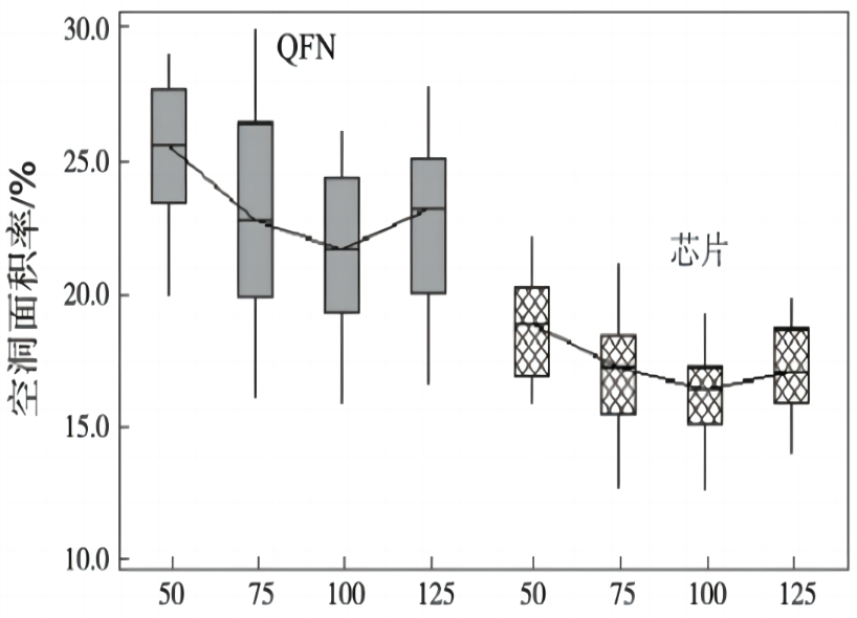
So sánh các lỗ trên lưới thép có độ dày khác nhau
3.3 Tỷ lệ diện tích khoang hàn và lỗ lưới thép
Lưới thép in có độ mở 100%, 90% và 80% đã được thử nghiệm, các điều kiện khác không thay đổi. Sau khi hàn lại, diện tích khoang của lớp hàn được đo và so sánh với lưới thép in với tỷ lệ mở 100%. Người ta nhận thấy rằng không có sự khác biệt đáng kể về khoang của lớp hàn trong điều kiện tỷ lệ mở 100% và 90% 80%, như trong Hình 8.
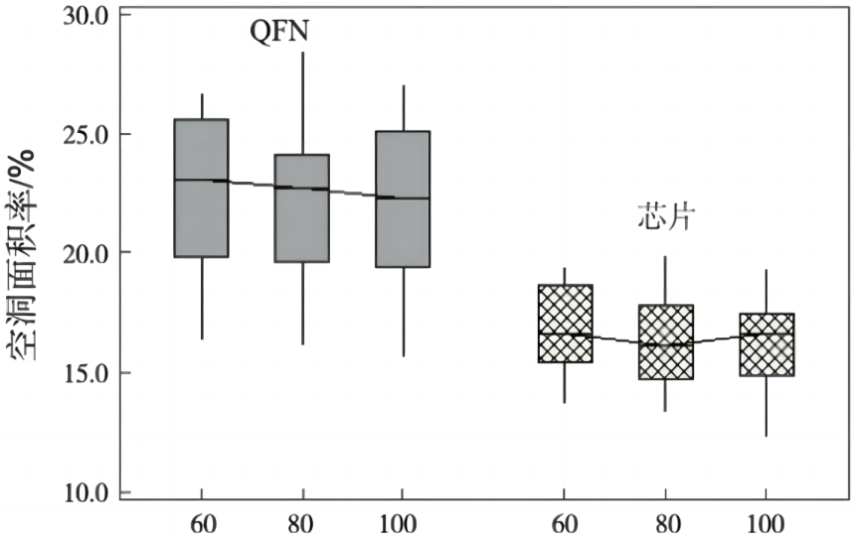
So sánh khoang của khu vực mở khác nhau của lưới thép khác nhau
3.4 Khoang hàn và hình lưới thép in
Với phép thử hình dạng in của miếng dán hàn dải b và lưới nghiêng c, các điều kiện khác không thay đổi. Sau khi hàn lại, diện tích khoang của lớp hàn được đo và so sánh với hình dạng in của lưới a. Người ta nhận thấy rằng không có sự khác biệt đáng kể về khoang của lớp hàn trong các điều kiện lưới, dải và lưới nghiêng, như trên Hình 9.
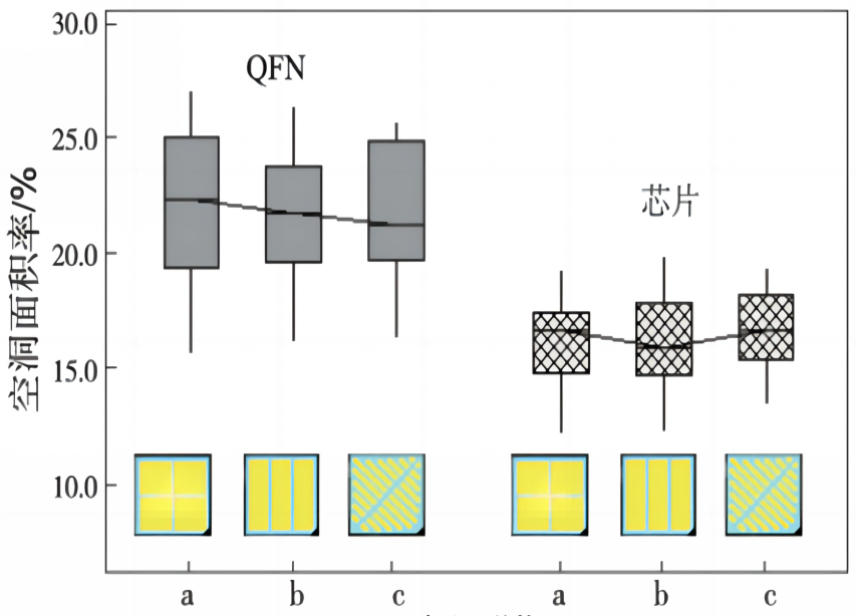
So sánh lỗ ở các chế độ mở khác nhau của lưới thép
3.5 Khoang hàn và thời gian hồi lưu
Sau khi thử nghiệm thời gian hồi lưu kéo dài (70 s, 80 s, 90 s), các điều kiện khác không thay đổi, đo lỗ thủng trên lớp hàn sau khi hồi lưu và so sánh với thời gian hồi lưu 60 s, nhận thấy rằng khi tăng thời gian hồi lưu, diện tích lỗ hàn giảm nhưng biên độ giảm giảm dần theo thời gian tăng, như trên Hình 10. Điều này cho thấy trong trường hợp thời gian hồi lưu không đủ, việc tăng thời gian hồi lưu có lợi cho không khí tràn hoàn toàn bọc trong nóng chảy thiếc lỏng, nhưng sau khi thời gian hồi lưu tăng lên đến một thời điểm nhất định, không khí bọc trong thiếc lỏng khó có thể tràn trở lại. Thời gian hồi lưu là một trong những yếu tố ảnh hưởng tới khoang hàn.
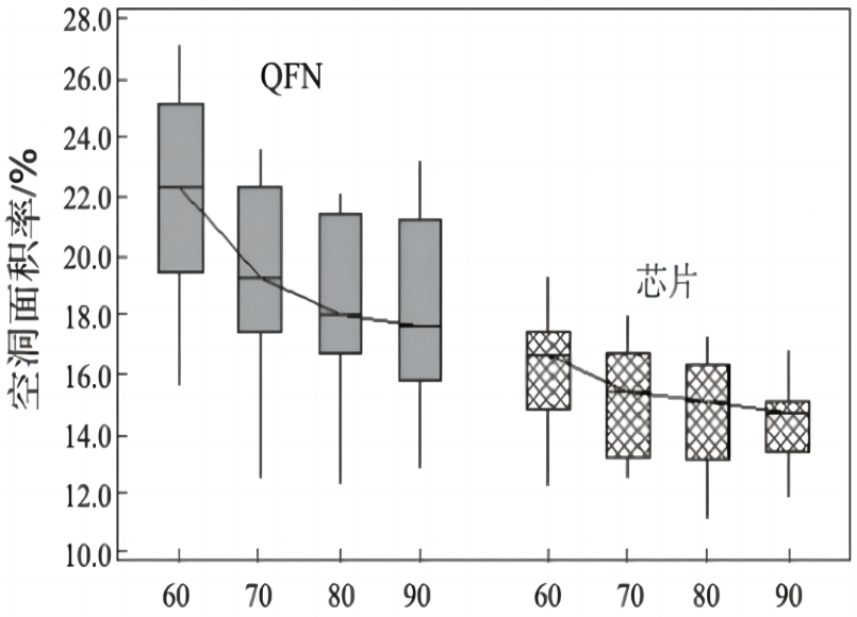
So sánh khoảng trống của các khoảng thời gian trào ngược khác nhau
3.6 Lòng hàn và nhiệt độ đỉnh lò
Với thử nghiệm nhiệt độ lò cao nhất 240oC và 250oC và các điều kiện khác không thay đổi, diện tích khoang của lớp hàn được đo sau khi nung chảy lại và so sánh với nhiệt độ lò cao nhất 260oC, người ta nhận thấy rằng trong các điều kiện nhiệt độ lò cao điểm khác nhau, khoang của lớp hàn của QFN và chip không thay đổi đáng kể, như trong Hình 11. Nó cho thấy nhiệt độ đỉnh lò khác nhau không có ảnh hưởng rõ ràng đến QFN và lỗ trên lớp hàn của chip, đây không phải là yếu tố ảnh hưởng.
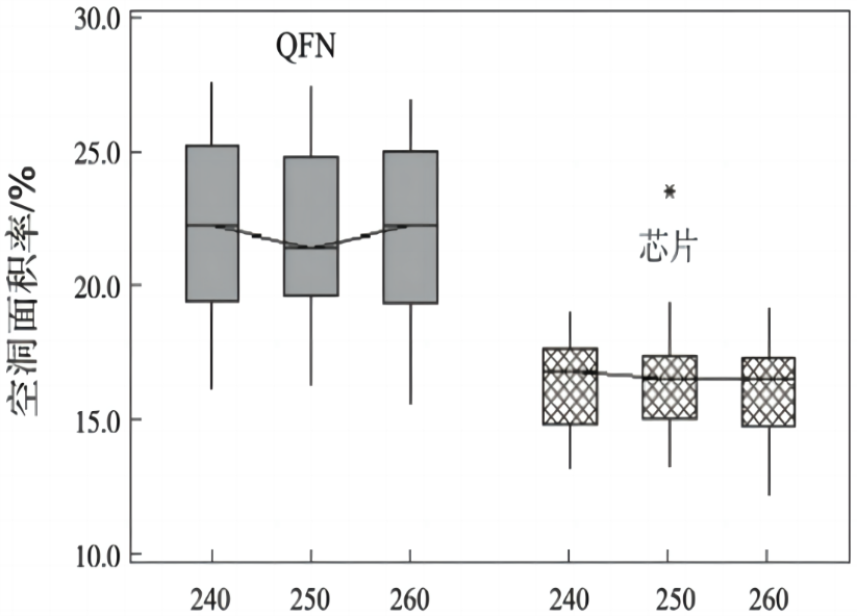
So sánh khoảng trống của nhiệt độ cao điểm khác nhau
Các thử nghiệm trên cho thấy các yếu tố quan trọng ảnh hưởng đến khoang lớp hàn của QFN và phoi là thời gian hồi lưu và độ dày lưới thép.
4 Hàn dán in cải thiện khoang hàn nóng chảy
Kiểm tra 4.1DOE để cải thiện khoang hàn
Lỗ thủng trên lớp hàn của QFN và chip được cải thiện bằng cách tìm ra giá trị tối ưu của các yếu tố ảnh hưởng chính (thời gian hồi lưu và độ dày lưới thép). Kem hàn là SAC305 loại 4, hình dạng lưới thép là loại lưới (độ mở 100%), nhiệt độ lò cao nhất là 260oC và các điều kiện thử nghiệm khác giống như của thiết bị thử nghiệm. Kết quả và thử nghiệm DOE được thể hiện ở Bảng 3. Ảnh hưởng của độ dày lưới thép và thời gian hồi lưu đến QFN và lỗ hàn chip được thể hiện trên Hình 12. Qua phân tích tương tác các yếu tố ảnh hưởng chính cho thấy sử dụng lưới thép có độ dày 100 μm và thời gian hồi lưu 80 giây có thể làm giảm đáng kể khoang hàn của QFN và chip. Tỷ lệ khoang hàn của QFN giảm từ mức tối đa 27,8% xuống 16,1% và tỷ lệ khoang hàn của chip giảm từ mức tối đa 20,5% xuống 14,5%.
Trong thử nghiệm, 1000 sản phẩm được sản xuất trong điều kiện tối ưu (độ dày lưới thép 100 μm, thời gian hồi lưu 80 giây) và tốc độ khoang hàn 100 QFN và chip được đo ngẫu nhiên. Tỷ lệ khoang hàn trung bình của QFN là 16,4% và tỷ lệ khoang hàn trung bình của chip là 14,7%. Tỷ lệ khoang hàn của chip và chip giảm rõ rệt.
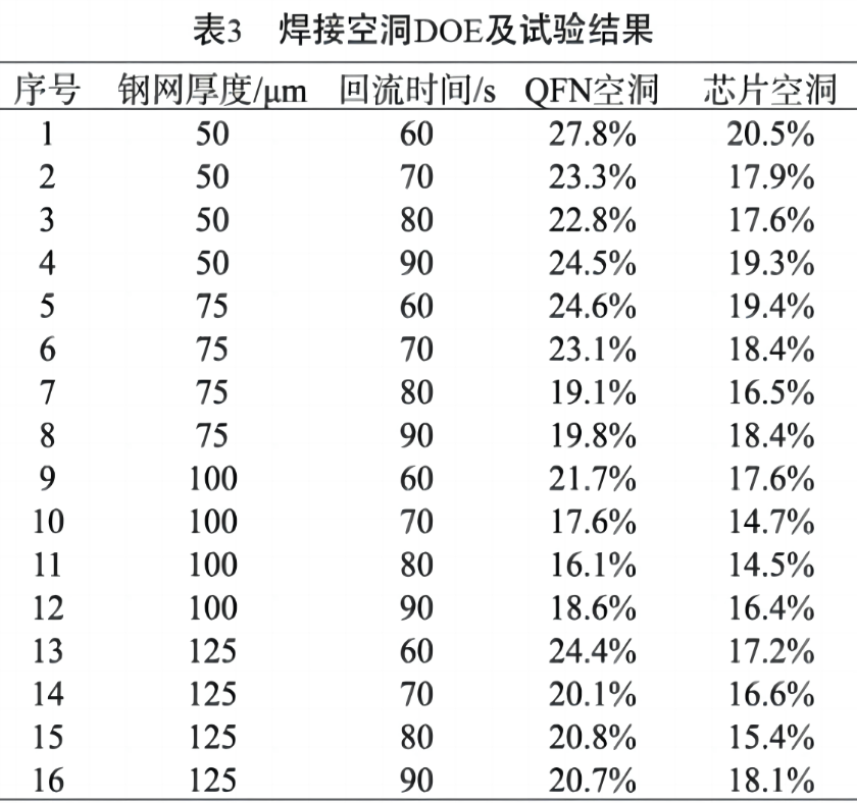
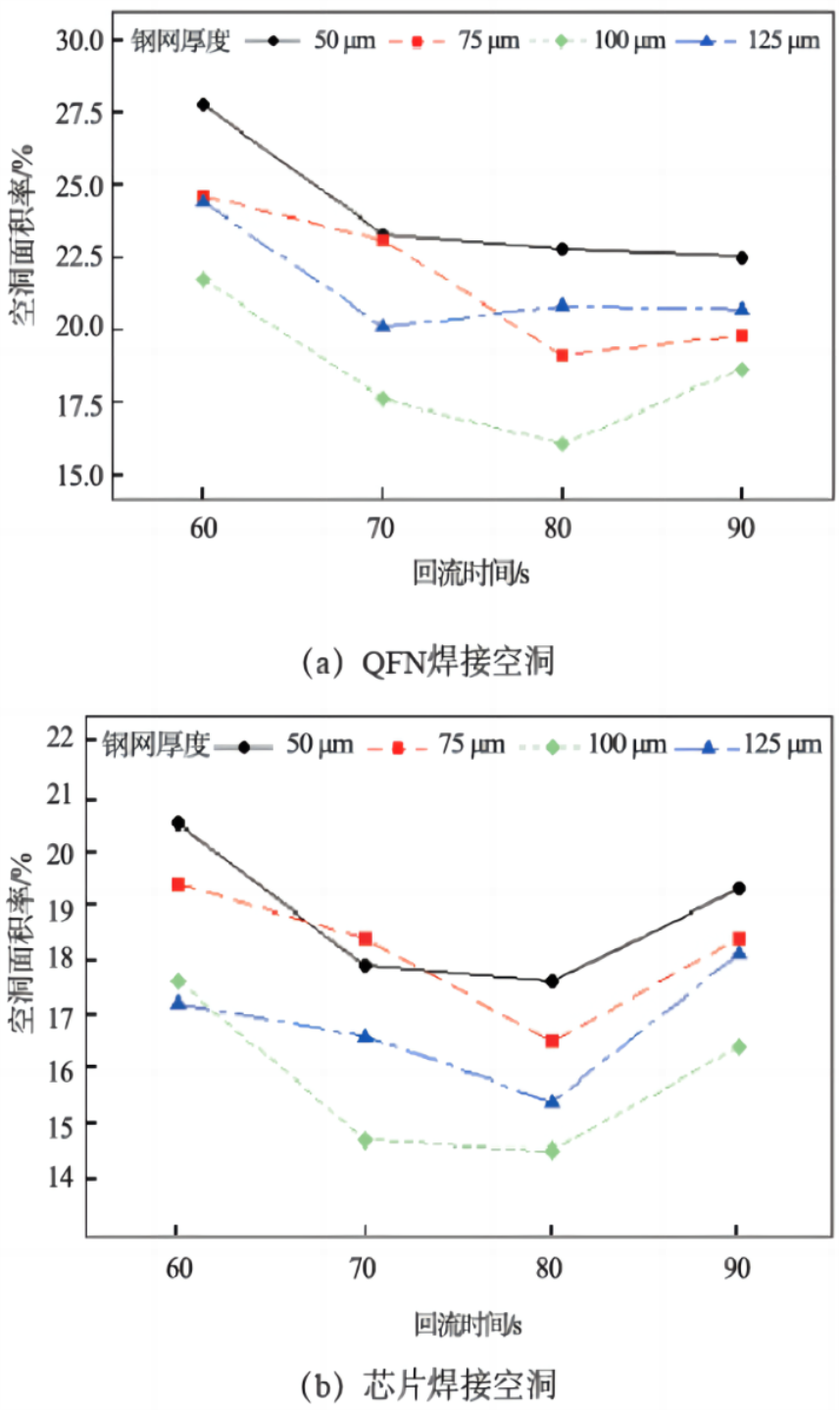
4.2 Quy trình mới cải thiện khoang hàn
Tình hình sản xuất và thử nghiệm thực tế cho thấy khi diện tích khoang hàn ở đáy chip nhỏ hơn 10% thì vấn đề nứt vị trí khoang chip sẽ không xảy ra trong quá trình liên kết và đúc chì. Các thông số quy trình được DOE tối ưu hóa không thể đáp ứng yêu cầu phân tích và giải quyết các lỗ trong phương pháp hàn nóng chảy dán hàn thông thường và tốc độ diện tích khoang hàn của chip cần phải giảm hơn nữa.
Vì chip được phủ trên vật hàn ngăn không cho khí trong vật hàn thoát ra ngoài nên tỷ lệ lỗ thủng ở đáy chip sẽ giảm hơn nữa bằng cách loại bỏ hoặc giảm lượng khí phủ vật hàn. Một quy trình hàn nóng chảy lại mới với hai in dán hàn được áp dụng: một in dán hàn, một nóng chảy lại không bao gồm QFN và chip trần xả khí trong hàn; Quy trình cụ thể của in dán hàn thứ cấp, vá và hồi lưu thứ cấp được thể hiện trong Hình 13.
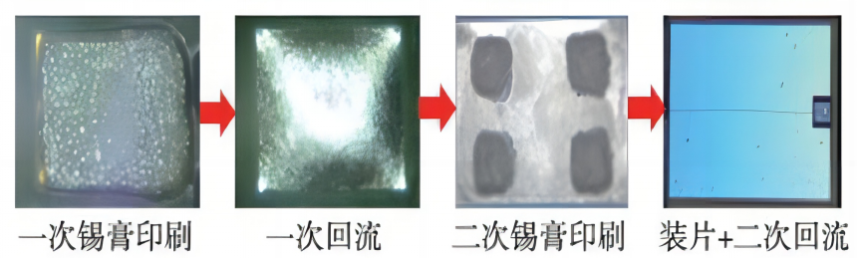
Khi miếng dán hàn dày 75μm được in lần đầu tiên, phần lớn khí trong chất hàn không có vỏ chip sẽ thoát ra khỏi bề mặt và độ dày sau khi hồi lưu là khoảng 50μm. Sau khi hoàn thành quá trình hồi lưu sơ cấp, các ô vuông nhỏ được in trên bề mặt vật hàn đã đông đặc đã nguội (để giảm lượng chất hàn, giảm lượng khí tràn, giảm hoặc loại bỏ vết hàn) và chất hàn có độ dày 50 μm (kết quả thử nghiệm ở trên cho thấy 100 μm là tốt nhất, do đó độ dày của bản in thứ cấp là 100 μm.50 μm=50 μm), sau đó lắp chip vào, sau đó quay trở lại 80 giây. Hầu như không có lỗ trên vật hàn sau lần in đầu tiên và hàn lại, miếng dán hàn ở lần in thứ hai nhỏ và lỗ hàn nhỏ, như trong Hình 14.
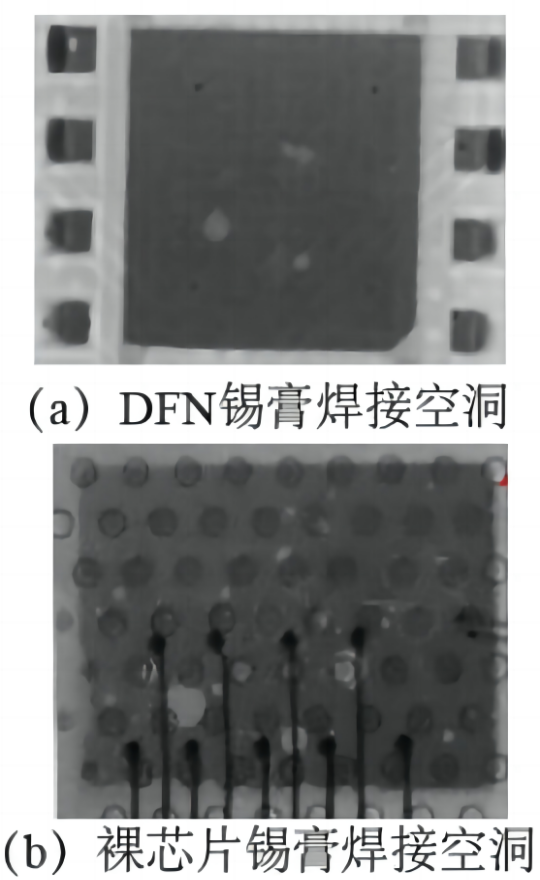
Sau hai lần in hàn dán, vẽ rỗng
4.3 Kiểm tra hiệu ứng khoang hàn
Sản xuất 2000 sản phẩm (độ dày của lưới thép in thứ nhất là 75 μm, độ dày của lưới thép in thứ hai là 50 μm), các điều kiện khác không thay đổi, đo ngẫu nhiên 500 QFN và tốc độ khoang hàn chip, nhận thấy rằng quy trình mới sau lần hồi lưu đầu tiên không có khoang, sau lần hồi lưu thứ hai QFN Tỷ lệ khoang hàn tối đa là 4,8% và tỷ lệ khoang hàn tối đa của chip là 4,1%. So với quy trình hàn in dán đơn ban đầu và quy trình được tối ưu hóa DOE, khoang hàn đã giảm đáng kể, như trong Hình 15. Không tìm thấy vết nứt phoi nào sau khi kiểm tra chức năng của tất cả các sản phẩm.
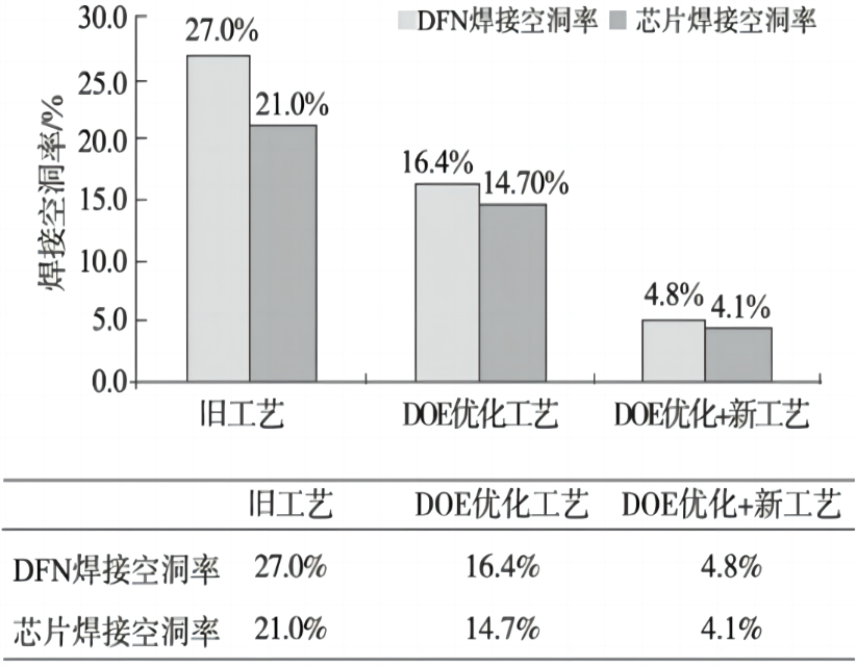
5 Tóm tắt
Việc tối ưu hóa lượng in dán hàn và thời gian hồi lưu có thể làm giảm diện tích khoang hàn, nhưng tốc độ khoang hàn vẫn lớn. Sử dụng hai kỹ thuật hàn nóng chảy in dán hàn có thể hiệu quả và tối đa hóa tỷ lệ khoang hàn. Diện tích hàn của chip trần mạch QFN có thể lần lượt là 4,4mm x4,1mm và 3,0mm x2,3mm trong sản xuất hàng loạt. Tốc độ khoang hàn nóng chảy lại được kiểm soát dưới 5%, giúp cải thiện chất lượng và độ tin cậy của hàn nóng chảy lại. Nghiên cứu trong bài báo cung cấp một tài liệu tham khảo quan trọng cho việc cải thiện vấn đề khoang hàn của bề mặt hàn có diện tích lớn.
Thời gian đăng: Jul-05-2023